Unveiling the Intricacies of Computer Numerical Control (CNC) Technology
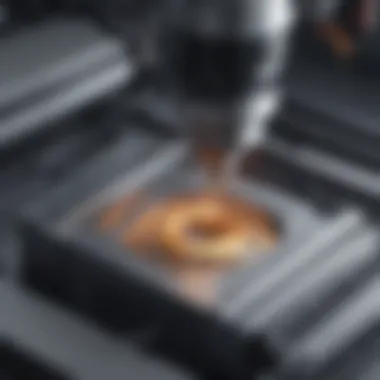
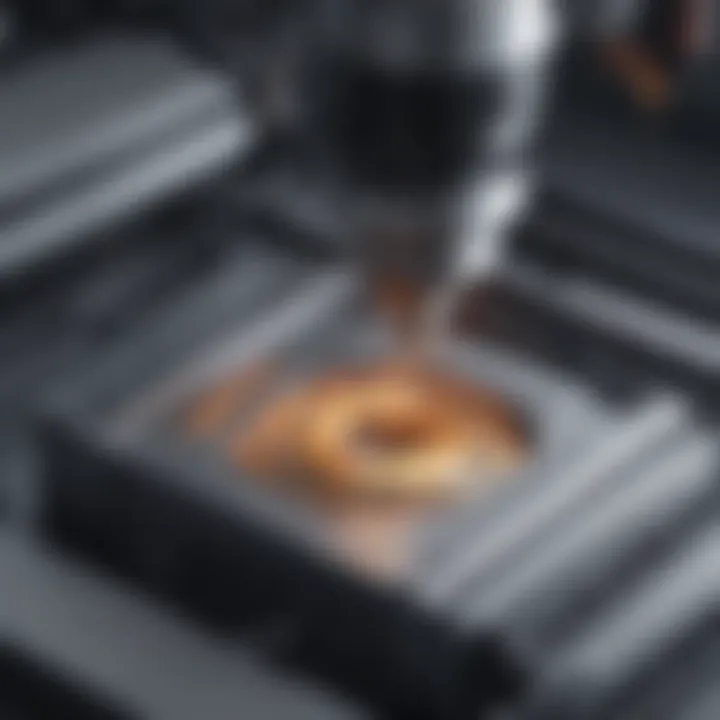
Introduction to Computer Numerical Control (CNC) Technology
In this section, we will embark on a profound journey into the realm of Computer Numerical Control (CNC) technology. Originating from the early days of industrial automation, CNC has evolved into a cornerstone of modern manufacturing processes. Our exploration begins by unraveling the historical tapestry behind CNC technology, tracing its roots back to its inception and tracing its transformative impact on industries worldwide. As we delve into the features and utility of CNC systems, we uncover their pervasive presence in various sectors, showcasing the versatility and significance of CNC technology in contemporary production landscapes.
Fundamental Principles and Applications
Within this segment, we uncover the fundamental principles underpinning CNC technology, demystifying its inner workings and intricate mechanisms. By elucidating concepts such as variables and data types, operators and expressions, and control structures, we lay the groundwork for comprehending the core elements of CNC programming. Expanding our inquiry, we explore the practical applications of CNC in diverse settings, from precision machining to intricate fabrication processes. Through insightful analyses and detailed examples, readers gain a holistic understanding of how CNC functions as a catalyst for innovation and efficiency in modern manufacturing.
Advanced Techniques and Innovations
Venturing into the domain of advanced CNC methodologies, we dissect the intricacies of functions and methods, shedding light on sophisticated programming techniques that enhance precision and productivity. By delving into object-oriented programming and exception handling within the CNC context, we navigate through cutting-edge approaches that bolster capabilities and expand horizons in the realm of digital fabrication. Through thought-provoking discussions and nuanced explorations, we unravel the complexities of leveraging advanced CNC techniques to maximize operational outcomes and stay at the forefront of technological advancements.
Practical Implementation and Hands-On Experience
This section embarks on a practical odyssey into the realm of CNC programming, offering readers tangible insights through a series of hands-on examples. By showcasing simple programs, intermediate projects, and code snippets, we provide a practical framework for applying theoretical knowledge to real-world scenarios. Through step-by-step guidance and immersive demonstrations, readers acquire essential skills and confidence to engage with CNC programming actively. As we bridge the gap between theory and practice, this segment serves as a gateway to honing programming proficiency and fostering a hands-on approach to mastering CNC technology.
Learning Resources and Continued Education
Concluding our discourse, we present a curated selection of resources and avenues for further learning in the realm of CNC technology. From recommended books and tutorials to online courses and platforms dedicated to CNC programming, we equip readers with the tools and guidance necessary to deepen their expertise and expand their knowledge horizons. By delving into community forums and groups focused on CNC technology, we foster collaboration, mentorship, and continuous learning within a vibrant ecosystem of enthusiasts and experts. Through these enriching resources, readers can cultivate their passion for CNC technology and embark on a journey of lifelong learning and skill development.
Introduction to CNC Technology
In the realm of modern manufacturing, Computer Numerical Control (CNC) technology stands as a pivotal force reshaping industries. As we embark on a journey to unravel the intricate workings of CNC, it becomes evident that its impact is far-reaching and transformative. From revolutionizing machining processes to enhancing precision and automation, the realm of CNC technology opens up a world of possibilities for innovative production methods.
Definition of Computer Numerical Control (CNC)
Evolution of CNC Systems
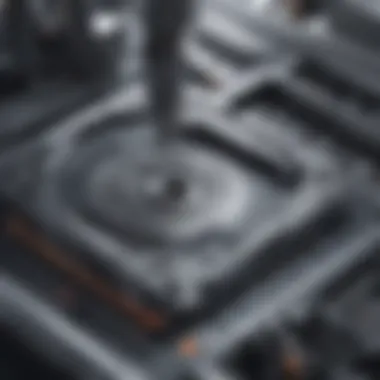
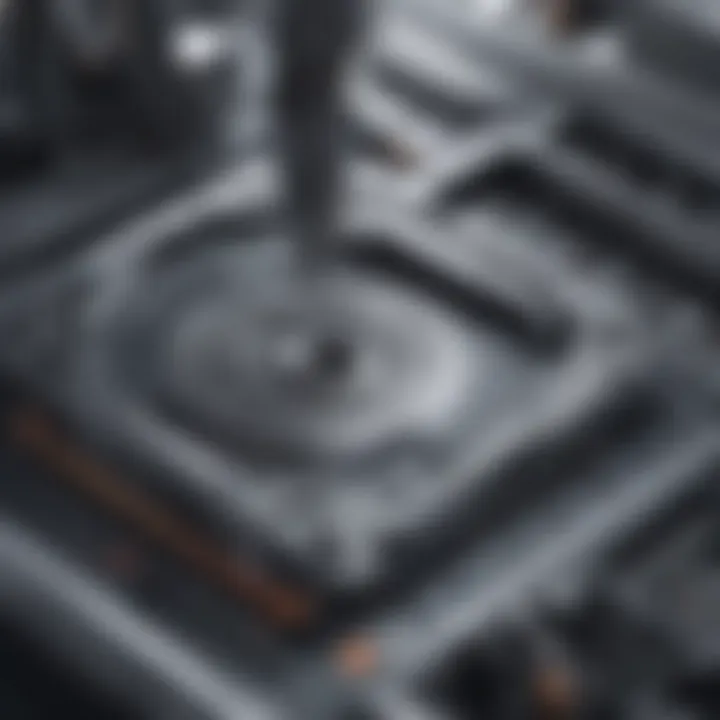
The evolution of CNC systems marks a significant milestone in the history of manufacturing. By tracing back to its origins, we uncover a gradual shift from manual operations to computerized control, revolutionizing the efficiency and accuracy of machining processes. The key characteristic of this evolution lies in its ability to streamline production, reduce human error, and pave the way for automated workflows. While its advantages are apparent in enhancing productivity and consistency, careful consideration must be given to the initial setup costs and training requirements inherent in adopting CNC systems.
Basic Components of CNC Machines
Delving into the basic components of CNC machines unveils a structured framework essential for their functionality. From spindle motors to control panels, each component plays a crucial role in executing precise machining operations. The key characteristic of these components lies in their interconnectivity, working harmoniously to translate digital instructions into physical outputs with unparalleled accuracy. While their benefits include improved efficiency and repeatability, challenges such as maintenance costs and technical complexities underscore the need for skilled operators to leverage the full potential of CNC machines.
Significance of CNC in Modern Manufacturing
Enhanced Precision and Accuracy
The pursuit of enhanced precision and accuracy drives the core of CNC technology's significance in modern manufacturing. By harnessing the power of computer-aided design and control algorithms, CNC systems excel in delivering intricate geometries with nanoscale accuracy. The key characteristic of precision machining lies in its ability to achieve tolerances beyond human capability, ensuring the production of flawless components for various industries. While the advantages are evident in quality enhancement and waste reduction, challenges such as calibration intricacies and material limitations warrant meticulous attention in optimizing precision CNC processes.
Efficiency and Automation
Efficiency and automation form the cornerstone of CNC technology's impact on modern manufacturing practices. Through the integration of robotic arms and intelligent programming, CNC systems streamline production workflows, minimize idle times, and boost overall productivity. The key characteristic of this automation lies in its ability to operate 247 without fatigue, ensuring continuous output and timely deliveries. While the benefits encompass increased output rates and resource optimization, considerations such as cybersecurity risks and skill demands emphasize the importance of a holistic approach to implementing automated CNC solutions.
Core Concepts of CNC Technology
Understanding the core concepts of Computer Numerical Control (CNC) is paramount in grasping the essence of modern manufacturing processes. CNC technology operates based on precise instructions programmed into the system to control machinery and tools. It revolutionizes production by automating tasks, enhancing accuracy, and increasing efficiency. The key elements of CNC technology include its versatility in fabrication, the ability to produce complex shapes effortlessly, and the integration of software for seamless operation. By understanding these core concepts, individuals can appreciate how CNC systems have become indispensable in various industries.
Working Principles of CNC Systems
CNC Programming Languages
Discussing CNC programming languages sheds light on how instructions are communicated to CNC machines effectively. These languages play a crucial role in transforming design specifications into machine-readable code, guiding the tool's movements with precision. Common CNC programming languages include G-code and M-code, each with specific functions and syntax. Their significance lies in streamlining the manufacturing process, improving repeatability, and enabling customization based on project requirements.
CNC programming languages offer a structured approach to developing toolpaths, executing machining operations, and managing tool changes. Their ability to interpret complex geometric shapes, adjust cutting speeds, and monitor tool positions ensures consistent and accurate production outcomes. While these languages facilitate automation and reduce human error, mastering them requires comprehensive training and expertise to optimize machine performance.
Machining Operations
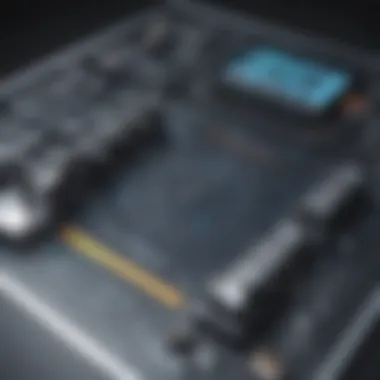
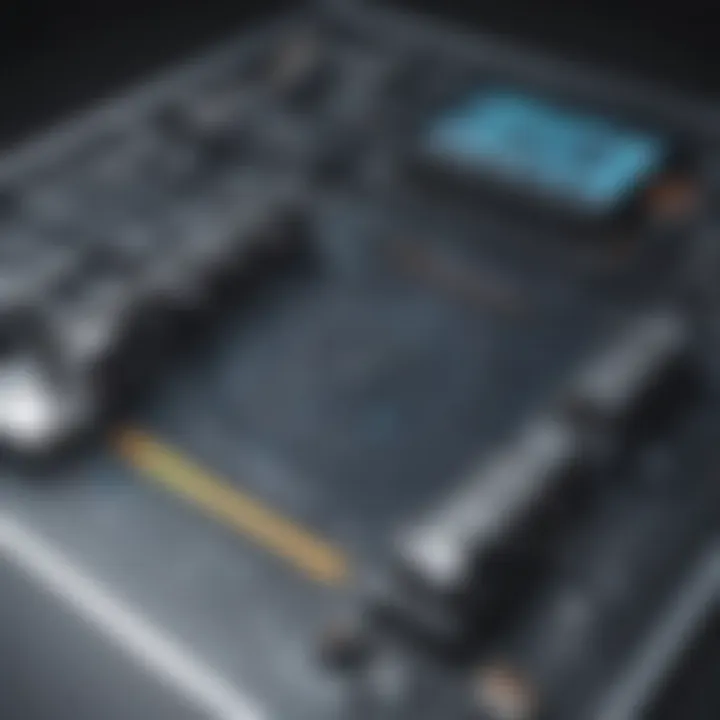
Exploring different machining operations in CNC systems reveals the diverse capabilities of these machines in shaping raw materials. Machining operations such as drilling, milling, turning, and grinding are core processes that shape workpieces into desired forms. Each operation requires specific tools, techniques, and parameters to achieve precise dimensional accuracy and surface finishes.
The key characteristic of machining operations lies in their adaptability to various materials, including metals, plastics, and composites. CNC machines excel in high-speed machining, multitasking capabilities, and multi-axis operations, enhancing productivity and reducing production lead times. However, mitigating heat generation, tool wear, and vibrations are critical considerations to ensure optimal machining performance.
Types of CNC Machines
CNC Milling Machines
Delving into CNC milling machines unveils their versatility in executing a wide range of milling operations with utmost precision. These machines utilize rotary cutters to remove material from a workpiece, creating intricate patterns, holes, or slots. The key characteristic of CNC milling machines lies in their ability to produce complex shapes and contours efficiently, making them ideal for prototyping and low-volume production.
CNC milling machines offer advantages such as high repeatability, geometric accuracy, and enhanced surface finish quality. Their flexibility in handling various tool sizes, spindle speeds, and workpiece materials expands their application across diverse industries. Despite their efficiency, tool deflection, chatter, and toolpath optimization present challenges that operators need to address for optimal milling performance.
CNC Lathes
Examining CNC lathes showcases their proficiency in turning operations, shaping workpieces with rotational symmetry. These machines secure the workpiece on a spindle and use cutting tools to remove excess material, creating cylindrical or conical shapes. The key characteristic of CNC lathes lies in their precision turning capabilities, offering high accuracy and repeatability in producing components.
CNC lathes excel in continuous high-volume production, rapid material removal rates, and improved surface finish quality. Their ability to perform facing, grooving, threading, and taper turning operations enhances manufacturing efficiency. However, considerations such as tool geometries, cutting parameters, and vibration damping techniques are essential to maximize turning performance.
Applications of CNC Technology
In the realm of modern manufacturing, the application of CNC (Computer Numerical Control) technology is nothing short of revolutionary. Its precision and efficiency have redefined production processes across various industries, showcasing the importance of embracing technological advancements. CNC technology plays a vital role in enhancing productivity, ensuring consistent quality, and enabling mass customization that was once deemed unattainable. With its integration, manufacturers can achieve intricate designs and complex geometries with unparalleled accuracy and speed, opening new frontiers in innovation and competitiveness.
Automotive Industry
Precision Machining of Components
The precision machining of components within the automotive sector epitomizes the pinnacle of accuracy and meticulous craftsmanship. This aspect focuses on fabricating intricate parts with micron-level precision, guaranteeing optimal functionality and durability of the final product. By utilizing CNC technology, automotive manufacturers can achieve tight tolerances, smooth finishes, and complex geometries that were previously challenging to attain through traditional machining methods. The meticulous attention to detail in precision machining ensures that each component fits seamlessly into the assembly, enhancing the vehicle's performance and reliability.
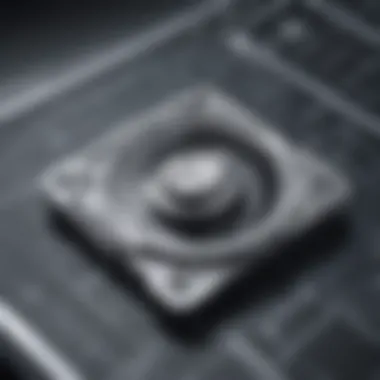
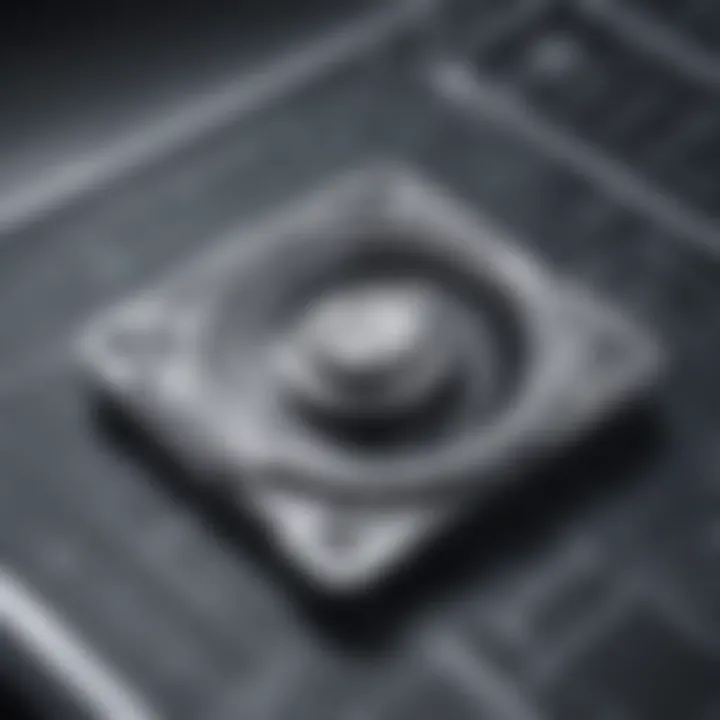
Customized Part Production
Customized part production stands as a hallmark of CNC technology in the automotive industry, offering flexibility and adaptability to meet evolving consumer demands. This facet emphasizes the ability to produce bespoke components tailored to specific requirements, whether for performance enhancements, aesthetic customization, or functional modifications. CNC machining enables swift prototyping and iterative design processes, facilitating rapid development cycles and reducing time-to-market for custom automotive parts. The customization options available through CNC technology empower manufacturers to cater to niche markets, personalize products, and elevate the overall customer experience.
Aerospace Sector
Complex Part Manufacturing
Within the aerospace sector, complex part manufacturing showcases the intricate capabilities of CNC technology in fabricating high-precision components for aircraft and space systems. This specialized area focuses on producing geometrically challenging parts with strict adherence to aerospace standards and regulations. CNC machining excels in crafting intricate structures, specialized materials, and intricate geometries required for aerospace applications, ensuring reliable performance under extreme conditions. The precision and repeatability offered by CNC technology are pivotal in meeting the stringent requirements of the aerospace industry, where safety and quality are uncompromising priorities.
High-Tolerance Machining
High-tolerance machining exemplifies the pursuit of perfection in aerospace component fabrication, where deviations in dimensions can have critical implications on flight performance and safety. This aspect prioritizes producing parts with minimal error margins, exceptional surface finishes, and impeccable dimensional accuracy to meet aerospace specifications. CNC technology plays a pivotal role in achieving ultra-precise tolerances, ensuring every component meets the stringent criteria set forth by regulatory bodies and aircraft manufacturers. The high-tolerance machining capabilities of CNC systems instill confidence in aerospace engineers and manufacturers, assuring that each part meets the rigorous standards governing the aerospace sector.
Future Trends and Innovations in CNC
The section on Future Trends and Innovations in CNC technology is crucial in this article as it sheds light on the upcoming advancements and developments in the field. Understanding the future trends is essential for professionals in the manufacturing industry to stay ahead of the curve and adapt to technological changes. By focusing on this aspect, readers can comprehend the direction in which CNC technology is headed and the potential impact on manufacturing processes.
Integration of AI in CNC Systems
Machine Learning Algorithms
When delving into Machine Learning Algorithms within CNC systems, it is imperative to grasp their specific role in enhancing automation and efficiency. These algorithms are designed to enable machines to learn from data and improve their performance over time. The key characteristic of Machine Learning Algorithms lies in their ability to analyze patterns and make predictions without explicit programming, thereby enhancing the adaptability of CNC systems. This feature makes Machine Learning Algorithms a popular choice in the realm of CNC technology, offering a unique approach to optimizing operations. However, it is essential to consider both the advantages and disadvantages of these algorithms, such as the potential for increased accuracy and productivity but also the requirement for extensive initial data training.
Predictive Maintenance
Discussing Predictive Maintenance within CNC systems unveils its vital contribution to preventing machine downtime and optimizing production schedules. This proactive approach involves using data analysis to predict when maintenance is required, thereby reducing unexpected failures and minimizing disruptions. The key characteristic of Predictive Maintenance is its ability to anticipate issues before they occur, ensuring continuous operation and prolonging machine lifespan. This approach is considered beneficial in CNC systems as it allows for planned maintenance, leading to efficient resource allocation. While the unique feature of Predictive Maintenance lies in its preventive nature, it is crucial to acknowledge the associated advantages like cost savings and improved machine reliability, alongside challenges such as implementation costs and data accuracy.
Industry 4. and Smart Manufacturing
Exploring the realm of Industry 4.0 and Smart Manufacturing underlines the integration of technology for enhanced operational efficiency and productivity. This topic focuses on the adoption of Io T-enabled CNC Machines and Real-time Data Analytics to optimize manufacturing processes and enable data-driven decision-making in real-time. By incorporating IoT-enabled CNC Machines, manufacturers can achieve interconnected systems that enhance communication and data exchange, leading to improved coordination and resource utilization. This choice is beneficial in the context of this article as it aligns with the theme of technological innovation and automation within CNC systems. The unique feature of IoT-enabled CNC Machines lies in their ability to gather and transmit data for predictive analysis, shaping a more streamlined production environment. While the advantages include enhanced connectivity and scalability, challenges may arise in terms of cybersecurity and data privacy.
Real-time Data Analytics
When examining Real-time Data Analytics in the context of CNC technology, emphasis should be placed on its role in providing actionable insights for decision-making. This approach involves analyzing data as it is generated, enabling manufacturers to monitor processes instantaneously and make informed adjustments. The key characteristic of Real-time Data Analytics lies in its ability to offer up-to-the-minute information, facilitating quick responses to production variations and ensuring optimal efficiency. Adopting this approach is advantageous for CNC systems as it promotes agile decision-making and performance optimization. The unique feature of Real-time Data Analytics is its capacity to facilitate predictive modeling and trend identification, empowering manufacturers to address potential issues promptly. While the benefits include enhanced operational visibility and productivity, challenges may emerge in terms of data accuracy and system integration.