Unveiling the Intricate Composition of Bronze: A Dive into Its Elemental Makeup and Properties
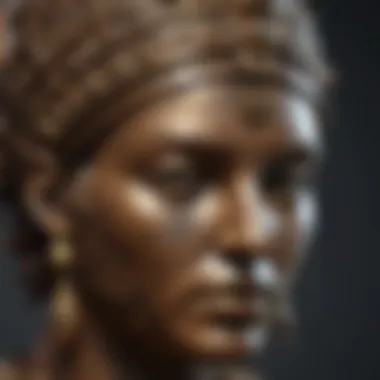
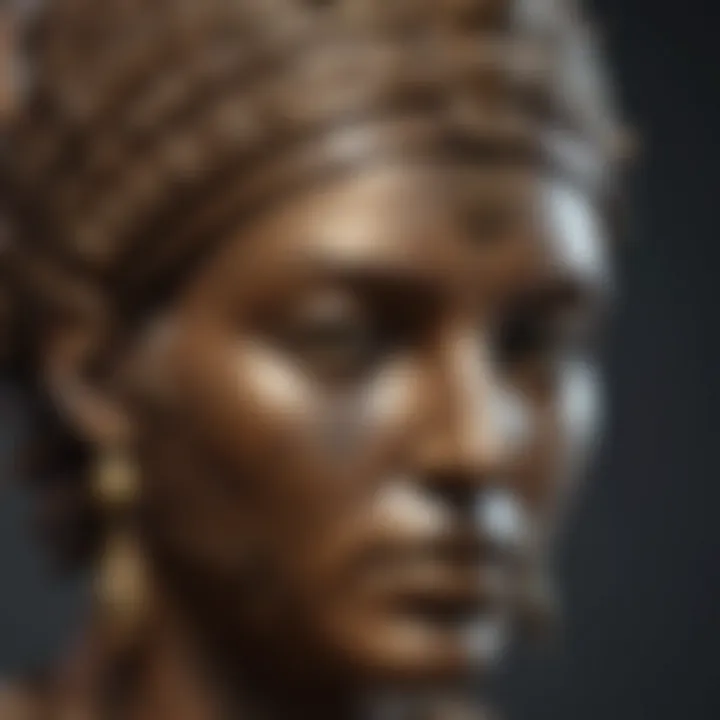
Introduction to the Composition of Bronze
Bronze is an alloy that has captured the fascination of historians, metallurgists, and craftsmen for centuries. Understanding its composition is key to appreciating its historical significance and its enduring importance in various industries. This section will delve into the intricate blend of metals that form bronze and shed light on the elemental makeup and properties that set it apart from other materials.
Historical Significance
The history of bronze is deeply interwoven with the development of human civilization. From the Bronze Age to the present day, bronze has played a vital role in shaping art, tools, and cultural artifacts. By exploring the historical context of bronze production and usage, we can gain a deeper appreciation for this versatile alloy.
Elemental Composition
Bronze is primarily composed of copper and tin, with varying proportions that influence its properties. Additionally, trace elements such as lead, zinc, or phosphorus may be present in certain bronze alloys. Understanding the precise composition of bronze is crucial for achieving the desired characteristics in the final product.
Unique Properties
One of the key attractions of bronze is its unique combination of strength, durability, and malleability. Unlike pure copper, bronze is harder and less prone to corrosion, making it ideal for sculpting, casting, and creating intricate designs. By examining the properties of bronze in detail, we can uncover why it remains a preferred material in various industries.
Methods of Bronze Production
To create bronze, metallurgists employ traditional techniques such as smelting and casting. Smelting involves melting copper and tin together at high temperatures, ensuring a homogeneous blend. Casting allows craftsmen to pour the molten bronze into molds to create intricate shapes and designs. By exploring the methods of bronze production, we can appreciate the craftsmanship and skill required to forge this ancient alloy.
Smelting Process
The smelting process begins by heating copper and tin ores to extract the raw metals. These metals are then combined in specific ratios to achieve the desired bronze alloy. The smelting process requires precision and expertise to ensure the proper fusion of metals and the elimination of impurities.
Casting Techniques
Casting bronze involves pouring the molten alloy into molds to create sculptures, tools, or decorative items. Craftsmen use techniques such as lost-wax casting or sand casting to bring intricate designs to life. Each casting method requires careful attention to detail and a keen understanding of bronze's properties to achieve the desired results.
Finishing and Polishing
Once the bronze has been cast into its desired shape, artisans employ various finishing techniques to enhance its appearance. This may involve polishing the surface to achieve a lustrous shine or applying patinas to create unique color effects. By mastering the art of finishing and polishing bronze, craftsmen can transform raw metal into exquisite works of art.
Applications of Bronze
Bronze's versatility and durability make it a sought-after material in numerous industries, ranging from art and architecture to electronics and marine engineering. By exploring the diverse applications of bronze, we can understand why this ancient alloy continues to be relevant in the modern world.
Art and Sculpture
Bronze has long been favored by artists for its workability and ability to capture intricate details. Sculptors use bronze to create statues, reliefs, and monuments that withstand the test of time. The malleability of bronze allows artists to explore creative possibilities and bring their visions to life in lasting form.
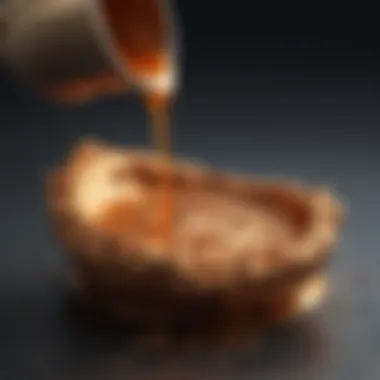

Industrial and Mechanical Uses
In industrial settings, bronze is valued for its strength, corrosion resistance, and heat conductivity. Bronze components are used in machinery, bearings, and electrical connectors due to their reliability and longevity. The unique properties of bronze make it an essential material in achieving optimal performance and durability in various mechanical applications.
Architectural Design
Architects and designers utilize bronze in constructing structures, facades, and decorative elements. Bronze's aesthetic appeal, along with its ability to withstand environmental conditions, makes it a preferred choice for architectural accents and sculptures. By incorporating bronze into architectural design, professionals can create striking visuals that stand the test of time.
Conclusion
Introduction to Bronze
Bronze, a historically significant alloy, holds a crucial place in various industries due to its unique composition and properties. This fascinating material, composed primarily of copper and tin, has withstood the test of time, showcasing remarkable strength and durability. Understanding the intricacies of bronze is essential to grasp its wide-ranging applications and importance in art, engineering, and beyond.
Definition of Bronze
Origins of Bronze
Bronze, originating in ancient times, marked a pivotal advancement in metallurgy. The fusion of copper and tin gave rise to a material stronger than its individual components, revolutionizing toolmaking and weaponry. The allure of bronze lies in its malleability and resistance to corrosion, making it a favored choice for artisans and craftsmen throughout history. Despite its susceptibility to tarnishing, bronze's rich history and cultural significance endure, cementing its place as a timeless alloy of choice.
Significance in History
The significance of bronze in history cannot be overstated. This alloy bridged civilizations and epochs, reshaping warfare, commerce, and art. The enduring legacy of bronze artifacts speaks volumes about its intrinsic value and symbolic importance. Whether adorning temples or forging weapons of war, bronze remains a hallmark of human ingenuity and craftsmanship. Its ability to embody strength, beauty, and cultural heritage makes bronze an indispensable component of historical narratives and artistic endeavors.
Properties of Bronze
Strength and Durability
Bronze's exceptional strength and durability stem from its robust composition of copper and tin. This alloy surpasses pure copper in toughness and resilience, making it a preferred choice for structural applications and artistic creations. The marriage of these metals imbues bronze with a balance of rigidity and ductility, allowing for intricate designs and lasting endurance. Despite its superior strength, bronze's workability and aesthetic appeal set it apart as a versatile material prized for its enduring quality.
Corrosion Resistance
An inherent advantage of bronze lies in its natural resistance to corrosion. Unlike iron and steel counterparts, bronze exhibits a remarkable ability to withstand oxidation and environmental degradation. This innate property makes bronze a durable and low-maintenance material suitable for outdoor sculptures, marine equipment, and architectural embellishments. The protective patina that forms on bronze surfaces acts as a shield against corrosive elements, preserving its luster and structural integrity over time.
Composition of Bronze
Main Elements in Bronze
Copper
bronze owes its foundational properties to copper, as it serves as the principal component in bronze alloys. The distinctive reddish-brown hue of copper interlaces with various elements to yield alloys with unique attributes. Copper's exceptional thermal and electrical conductivity, alongside its malleability, enrich the alloy with versatility and ductility. This section delves deep into the significance of copper in bronze formulations, outlining its indispensable role in shaping the alloy's structural integrity and ensuring longevity in a myriad of applications.
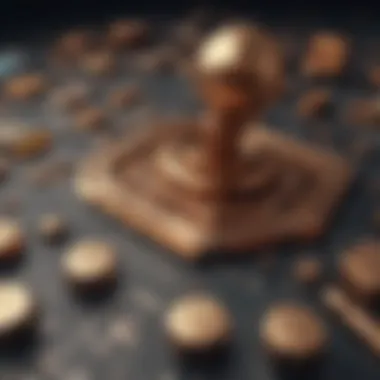
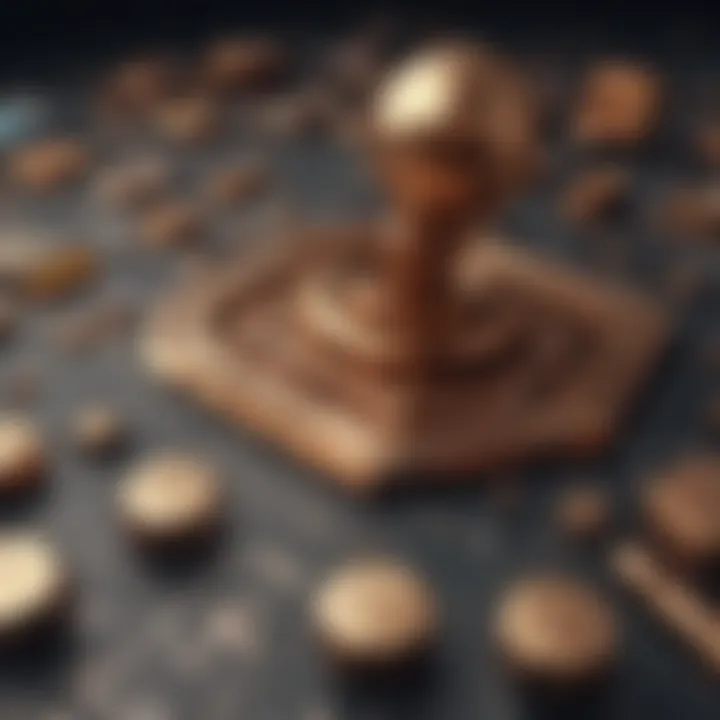
Tin
tin complements copper in bronze compositions to enhance its strength, hardness, and corrosion resistance. The addition of tin refines the microstructure of bronze alloys, contributing to their wear resistance and casting properties. The inclusion of tin alters the material's characteristics, such as hardness and machinability, making it a pivotal element in achieving desired mechanical properties and performance benchmarks. This section elucidates the strategic role of tin in fine-tuning the properties of bronze to meet specific industrial and creative demands.
Other Alloying Elements
beyond copper and tin, other alloying elements like zinc, lead, and phosphorus are incorporated into bronze formulations to modulate its characteristics. These elements impart unique traits like improved machinability, casting ability, or color variations to customized bronze alloys. Understanding the synergistic effects of these alloying additions is crucial in tailoring bronze alloys for specialized applications. This section elucidates the nuanced impact of other alloying elements on the overall properties and behavior of bronze, shedding light on the intricate balance required for optimal alloy performance.
Percentage Composition
Impact of Copper Content
the percentage of copper in bronze formulations significantly influences the alloy's mechanical and physical properties. Varying copper content can alter conductivity, hardness, and corrosion resistance, offering a spectrum of alloys with distinct features. This section dissects the implications of copper content on bronze alloys, highlighting the critical role of this elemental balance in defining the alloy's functionality and applicability across industries.
Effects of Tin Ratio
manipulating the tin ratio in bronze compositions introduces shifts in mechanical properties such as tensile strength and machinability. Fine-tuning the tin percentage enables manufacturers to customize bronze alloys for specific performance requirements, be it in structural applications or artistic endeavors. This section unpacks the nuanced effects of tin ratios on bronze properties, providing insights into the intricate interplay between alloy composition and material behavior.
Types of Bronze Alloys
The section on Types of Bronze Alloys delves into the diverse variants that contribute to the versatility and utility of bronze alloys. Exploring these variants sheds light on the specific elements, benefits, and considerations that add depth to our comprehension of bronze as a material. By understanding the distinctions between various bronze alloys, we can appreciate the nuanced applications and characteristics that each variant brings to the table.
Common Bronze Variants
- Phosphor Bronze:
Phosphor Bronze stands out as a crucial variant within the realm of bronze alloys due to its unique composition and properties. Its high phosphorus content lends it enhanced strength and wear resistance, making it a preferred choice in applications requiring durability and reliability. The key characteristic of Phosphor Bronze lies in its excellent machinability, which allows for intricate and precise detailing in components. This alloy's advantage in this article lies in its significance across industries that demand high-performance materials. Despite its advantages, one potential drawback of Phosphor Bronze is its relatively higher cost compared to other bronze alloys.
- Aluminum Bronze:
Aluminum Bronze is another noteworthy variant that contributes significantly to the overall landscape of bronze alloys. Known for its excellent corrosion resistance and elevated levels of strength, Aluminum Bronze serves as a popular choice in marine and architectural applications where exposure to harsh environments is a concern. The key feature of Aluminum Bronze is its exceptional weldability, making it a preferred option for fabricating complex structures. Its advantage in this article lies in its widespread use across industries that value the alloy's superior mechanical properties. However, one aspect that may be considered a disadvantage of Aluminum Bronze is its susceptibility to dezincification in certain environments.
Specialized Bronze Alloys
- Silicon Bronze:
Silicon Bronze emerges as a specialized alloy with distinct characteristics that cater to specific industrial needs. Its notable feature is its enhanced resistance to corrosion, making it a favorable choice in environments where exposure to moisture and chemicals is prevalent. The advantage of Silicon Bronze in this article is its exceptional aesthetic appeal, rendering it ideal for artistic and decorative applications. Despite its advantages, one potential downside of Silicon Bronze is its limited availability compared to more common bronze variants.
- Nickel Aluminum Bronze:
Nickel Aluminum Bronze represents a specialized alloy renowned for its superior mechanical properties and exceptional corrosion resistance. The key characteristic of Nickel Aluminum Bronze lies in its high tensile strength and toughness, making it suitable for demanding engineering applications. Its advantage in this article is its widespread utilization in marine and aerospace industries where performance under extreme conditions is imperative. However, one possible drawback of Nickel Aluminum Bronze is its higher cost compared to conventional bronze alloys.
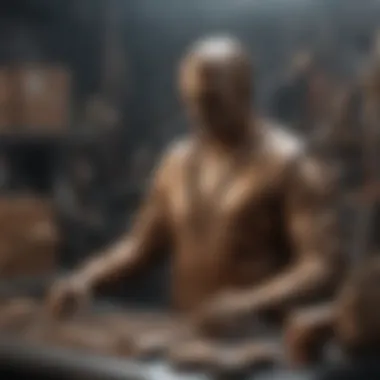
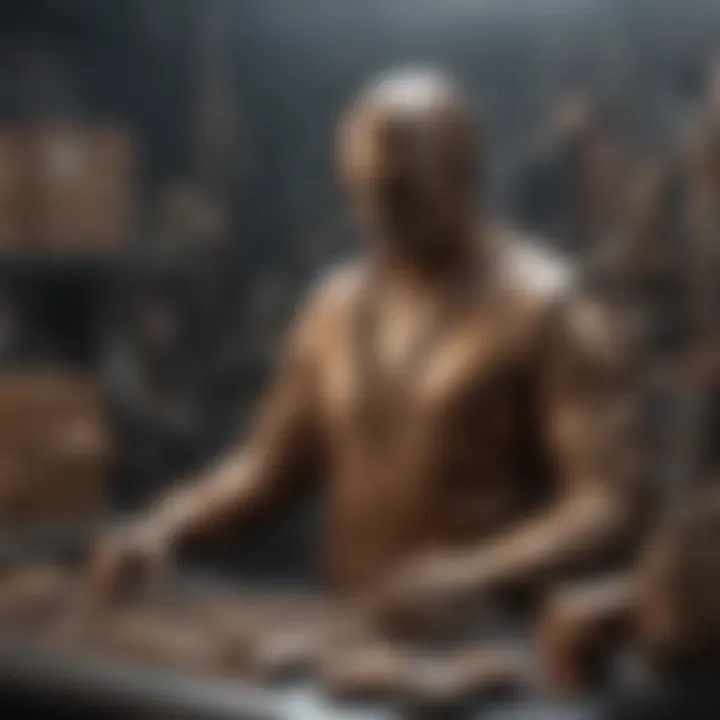
Production and Applications
Bronze's production and applications stand at the core of this article, pivotal to comprehending the alloy's utility and significance across various industries. Through meticulous exploration, we uncover the intricate processes involved in both creating and utilizing bronze, shedding light on its diverse applications. The production phase revolves around casting and forging techniques, each offering unique advantages and considerations for different applications.
Manufacturing Process
Casting
Casting plays a fundamental role in bronze production, allowing for intricate shapes and designs to be formed with precision. Its versatility and ability to replicate complex patterns make it a popular choice in the manufacturing industry. The key characteristic of casting lies in its capability to produce detailed and intricate bronze components efficiently. However, one must consider the limitations in terms of material waste and post-processing requirements, making it essential to strategize casting techniques to optimize cost and efficiency.
Forging
In contrast, forging emerges as a robust method for shaping bronze through controlled deformation. The key characteristic of forging is its capacity to enhance the material's strength and durability by aligning the internal grain structure. This makes forged bronze components ideal for applications requiring superior mechanical properties. A unique feature of forging is its ability to improve the structural integrity of bronze parts, albeit with a higher production cost compared to casting. Despite the cost consideration, forging offers unparalleled strength and resilience, making it a preferred choice for demanding applications.
Utilization of Bronze
Art and Sculpture
The utilization of bronze in art and sculpture underscores its aesthetic appeal and sustainability in creative endeavors. Artists and sculptors leverage bronze's malleability and captivating luster to craft intricate masterpieces that withstand the test of time. The key characteristic of bronze in art lies in its ability to capture intricate details and textures, adding depth and realism to sculptures. While its durability ensures longevity, artists need to consider the weight and cost implications of working with bronze, balancing artistic vision with practical constraints.
Engineering and Construction
Bronze's utilization in engineering and construction amplifies its role as a reliable structural material with exceptional mechanical properties. Its corrosion resistance and thermal conductivity make it suitable for various engineering applications, from bearings to architectural elements. The key characteristic of bronze in engineering lies in its ability to withstand harsh environmental conditions while maintaining structural integrity. However, practitioners must navigate the challenges of material cost and fabrication complexity when incorporating bronze into construction projects, emphasizing the need for meticulous planning and execution to leverage its benefits effectively.
Modern Applications and Innovations
Technological Advancements
Additive Manufacturing:
Additive Manufacturing, a pivotal aspect of modern applications of bronze, has redefined the production processes involved in working with this alloy. By utilizing advanced 3D printing techniques, Additive Manufacturing enables intricate and customized designs to be fabricated with unparalleled precision. The key characteristic of Additive Manufacturing lies in its ability to streamline production, reduce material wastage, and enhance design flexibility. This technique proves to be a highly beneficial choice for creating complex bronze components with intricate geometries, catering to the ever-evolving demands of various industries. Despite its advantages, some limitations of Additive Manufacturing include higher production costs and longer processing times, factors that need to be considered when choosing this method for manufacturing bronze components.
Composite Materials:
The integration of Composite Materials represents another significant advancement in the utilization of bronze within modern applications. Composite Materials combine bronze with other substances to create hybrid materials that exhibit enhanced mechanical properties and specific tailored characteristics. The key characteristic of Composite Materials is their ability to improve the overall performance and functionality of bronze components by adding strength, reducing weight, or enhancing corrosion resistance. This approach has gained popularity due to its effectiveness in creating lightweight and durable bronze products, making it a preferred choice for industries requiring high-performance materials. Despite its advantages, drawbacks of Composite Materials include potential delamination issues and complex manufacturing processes that need careful management.
Future Prospects
Looking ahead, the future prospects for bronze in modern applications and innovations appear promising and full of opportunities for growth and development. By focusing on sustainability initiatives and integration in emerging industries, bronze continues to make strides in aligning with contemporary demands while keeping true to its historic significance.
Sustainability Initiatives:
Sustainability initiatives play a crucial role in shaping the future of bronze applications, emphasizing the importance of eco-friendly practices and resource conservation. By adopting sustainable production methods and recycling programs, bronze manufacturers can reduce their environmental footprint and contribute to a more sustainable industry. The key characteristic of sustainability initiatives lies in their ability to promote responsible usage of materials, energy efficiency, and waste reduction. This approach is a popular choice for bronze applications as it aligns with the growing global focus on environmental sustainability. Despite its advantages, challenges of sustainability initiatives include initial implementation costs and potential resistance from traditional manufacturing practices that need to be addressed for widespread adoption.
Integration in Emerging Industries:
The integration of bronze in emerging industries signifies a shift towards diversifying the application of this alloy beyond conventional uses. By incorporating bronze into cutting-edge sectors such as renewable energy, aerospace, and healthcare, new possibilities for enhancing performance and innovation emerge. The key characteristic of integration in emerging industries is its ability to stimulate cross-industry collaborations, drive technological advancements, and foster creative solutions to complex problems. This trend is beneficial for bronze applications as it opens doors to novel opportunities and broader market penetration. Despite its advantages, challenges of integration in emerging industries include regulatory hurdles and technological adaptation requirements that necessitate careful planning and strategic partnerships.